Both prismatic cells and cylindrical cells are a type of lithium ion battery.
Prismatic cells are encapsulated in aluminum or steel hard shells, and the internal structure is a winding or lamination process. As a mainstream lithium ion battery form, prismatic cells are relatively flexible in size and have a larger capacity.
Cylindrical cells are the first lithium ion batteries to achieve large-scale production. They are made by winding the positive electrode, negative electrode and separator into a cylindrical shape in a specific order and enclosing them in a metal shell.
Regarding the differences between prismatic cells and cylindrical cells, let us take a detailed look at them through various comparisons.
Prismatic vs Cylindrical Cells
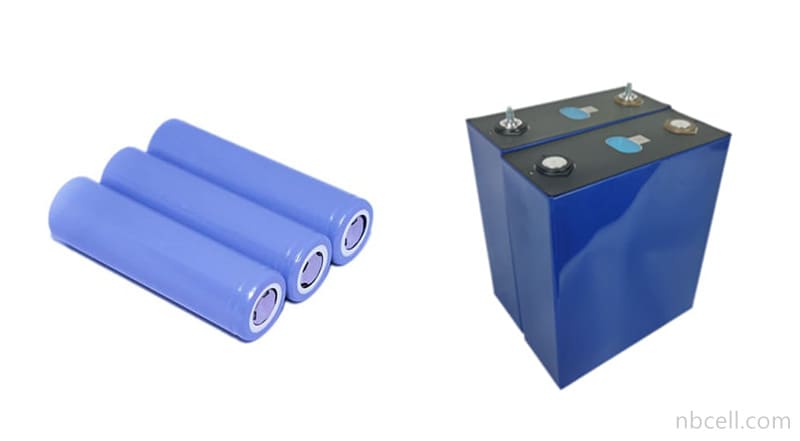
Appearance and Size
The most obvious difference between prismatic and cylindrical cells is the shape.
Prismatic cells are square in shape and vary in size. There are few universal sizes for prismatic cells, and each manufacturer has its own product design. Prismatic cells are relatively large in size and have higher capacity, making them more suitable for high-power applications. For a battery pack of the same voltage and capacity, prismatic battery require much fewer cells than cylindrical cells.
Cylindrical cells are cylindrical in shape, with common sizes such as 18650, 21700, and 4680. Cylindrical cells are usually small in size and suitable for applications with lower power requirements. As a result, their capacity is low, and multiple cylindrical cells need to be connected in parallel to increase capacity.
Manufacturing Process
Prismatic Cells Manufacturing Process
1. Shell manufacturing: The shell of prismatic cells is usually made of metal, such as aluminum alloy or stainless steel. The manufacturing process involves stamping, stretching and other processes. The stamping process requires extremely high mold precision to ensure the size consistency and surface flatness of the shell. The stretching process further shapes the depth and shape of the shell.
2. Battery cells assembly: After the positive and negative electrodes and diaphragms are stacked or wound into battery cells in sequence, they are carefully placed in the formed shell. The stacking process can improve the energy density and charge and discharge performance of the battery cells because it can reduce the resistance and mechanical stress inside the battery cells. The winding process is relatively more suitable for large-scale production and has higher production efficiency. After the battery cells assembly is completed, the electrolyte is injected.
3. Sealing and welding: To ensure the sealing and safety of the battery cells, the shell and the top cover are sealed by laser welding or resistance welding. Parameter control during the welding process is extremely critical. Any slight deviation may cause welding quality problems and affect the overall performance of the battery cells.
Cylindrical Cells Manufacturing Process
1. Shell molding: The shell of cylindrical cells is generally made of metal materials, and the seamless steel tube stretching process is mostly used. By stretching the metal tube in a specific mold, a cylindrical shell with a certain wall thickness and length is formed. Compared with the manufacturing of prismatic shells, the manufacturing process of cylindrical shells is relatively simple and has high production efficiency.
2. Battery cell winding: The cylindrical cells usually adopt the winding process. After the positive and negative plates and the diaphragm are alternately stacked, they are wound into cylindrical cells by a winding machine. During the winding process, the control of the winding tension is very critical. Excessive or insufficient tension will affect the internal structure and performance of the battery cell. At the same time, the speed and accuracy of winding are also directly related to the consistency and yield of the battery cells.
3. Sealing and assembly: After the battery cell is wound, the sealing and assembly process is carried out. In the sealing process, resistance welding is usually used to seal the top cover to the shell. The assembly process also includes assembling components such as the battery cell, electrolyte, and protection circuit into the shell to form a complete battery.
In terms of the complexity of the manufacturing process, the prismatic cell has the most complex manufacturing process due to its structural design and sealing process requirements. The cylindrical cell manufacturing process is relatively simple and has a high degree of standardization.
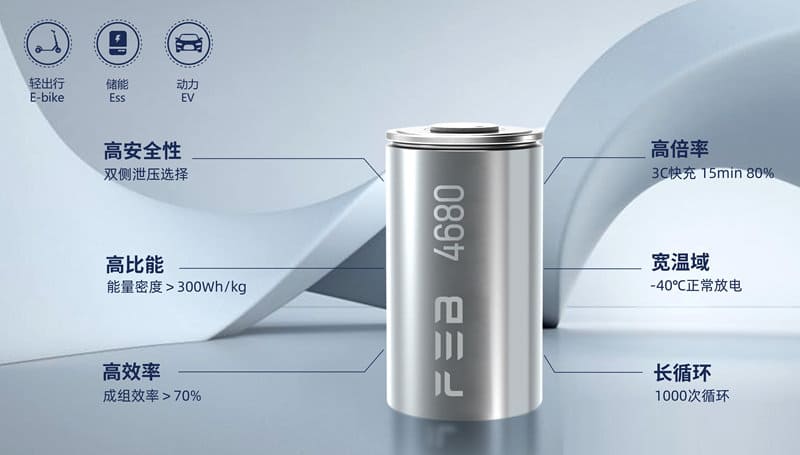
Energy Density
The energy density of cylindrical cells and prismatic cells is not only related to their structure and process, but more depends on their materials. And with the development of battery technology, whether it is cylindrical cells or prismatic cells, through continuous improvement of materials and processes, their single battery cell energy density is gradually increasing.
However, when manufacturing battery packs or battery systems, their overall energy density will change due to the selection of battery cells of different shapes.
Due to its square structure, thin shell and high packing efficiency, the volume energy density of the battery pack composed of prismatic cells is higher than that of cylindrical cells. The battery pack composed of cylindrical cells has a lower volume energy density than prismatic cells due to the heavy steel shell of the cylindrical cells and the large circular stacking gap. For example, Tesla’s 4680 large cylinder reduces the proportion of the shell by increasing the diameter of the single cell, and the single cell energy density is close to 300wh/kg, but the PACK-level volume density is still lower than that of prismatic batteries.
Safety
The prismatic cell shell structure has a strong bearing capacity, and the center temperature is easy to accumulate during large-capacity fast charging, so a complete thermal management system and safety design are needed to ensure high safety.
The cylindrical cell shell has high strength, built-in safety valve, and cylindrical design is more conducive to heat dissipation, and the single cell is safer. However, in extreme cases such as overcharging and short circuit, protective measures still need to be strengthened.
Production Costs
The manufacturing process of prismatic cell is relatively complex, with many customized molds and strict requirements on production equipment and process control. The production process of cylindrical cells is mature, with highly standardized product models and a high degree of commonality. This leads to fewer product specifications, fewer types of development of manufacturing molds, and stronger production line compatibility, which is in line with the “platform” production concept. Coupled with a high degree of automation, it significantly reduces the labor ratio of the production line and reduces labor costs. Therefore, under the same conditions, the production cost of cylindrical cells is lower than that of prismatic cells.
Cycle Life
The cycle life of prismatic cells is usually about 2000~4000 times. Prismatic cells used for energy storage can reach more than 6000 times. The cycle life of cylindrical cells is usually shorter.
So, in terms of cycle life, prismatic cells > cylindrical cells.
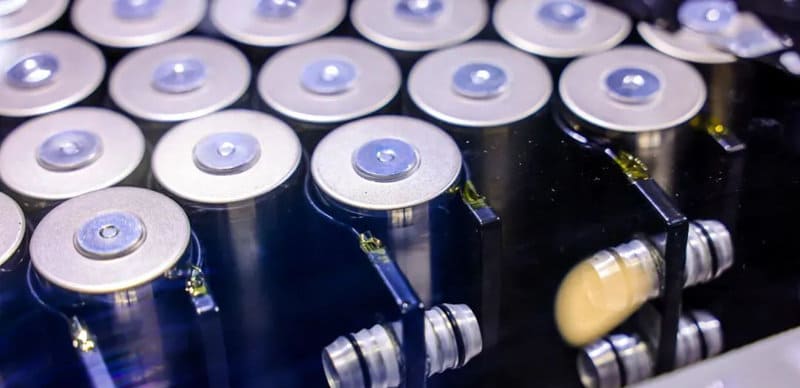
Space Utilization
When making lithium ion battery packs, cylindrical cells will form gaps when arranged, and the space utilization rate is about 70%. When prismatic cells are arranged, the gaps are eliminated, and the space utilization rate is over 80%, which is greatly improved.
Therefore, in terms of space utilization, prismatic cells > cylindrical cells.
Application
Prismatic cells are widely used in electric vehicles, energy storage systems and other fields. In electric vehicles, their compact structure can better fit the vehicle chassis space and improve the vehicle’s range and handling performance. In energy storage systems, prismatic cells with large capacity and long cycle life can better extend the service life of equipment, thereby reducing the cost of electricity per unit of the entire life cycle.
Cylindrical cells are often used in electric bicycles, medical equipment, consumer electronics and other fields. Their standardized size and good heat dissipation performance make product design and manufacturing more convenient. In the field of electric vehicles, some car companies such as Tesla also use cylindrical cells. However, due to the relatively small capacity of a single cylindrical cell, a large number of cylindrical cells need to be connected in series and parallel when used in electric vehicles, which increases the complexity and cost of the battery management system.
Summary
Through this article, I believe everyone has learned something about prismatic cells and cylindrical cells. In fact, no matter which form of lithium ion battery is chosen, the selection logic is mainly based on adaptability. After all, the one that suits your needs is the best.
I believe that with the continuous development of battery technology, both prismatic cells and cylindrical cells will continue to innovate in their respective areas of strength. They compete and complement each other, and the ultimate beneficiaries will be the entire battery ecosystem and the vast number of consumers.